When it comes to keeping motorists safe on the road, few inventions have had a bigger impact than the concrete Jersey barrier.
Jersey barriers, named for the state of New Jersey, were specifically designed to minimize damage to colliding vehicles (and the passengers inside) and prevent them from entering oncoming traffic. A few factors contribute to their unparalleled safety standards, including material, design, weight, and anchoring technique.
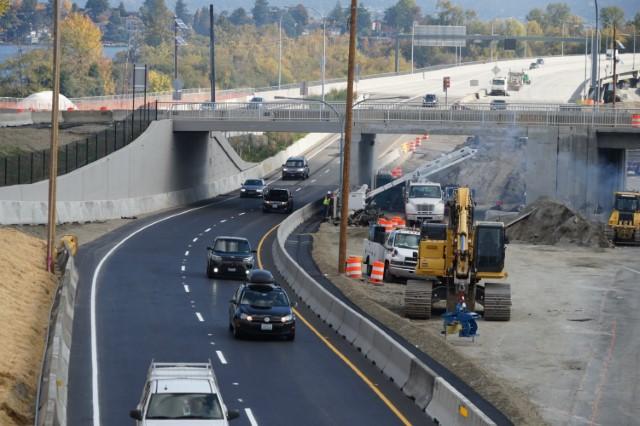
Material
Jersey barriers are made of reinforced concrete. This composite mix blends cement with water and aggregates such as sand or crushed gravel. This specific composition is highly durable and able to withstand significant compression loads, especially when reinforced with steel.
Alone, steel and concrete have weaknesses — steel cannot withstand significant compression, and concrete cannot handle much tension. But together these materials stand up to the force and impact of a vehicular collision.
Although Jersey barriers are durable, spalling is likely to occur while moving with machinery. Spalling refers to crumbling or breaking stone, which can break loose and become airborne during a high-impact collision. A Kenco Barrier Lift is recommended to increase the longevity of your barriers and reduce spalling over time.
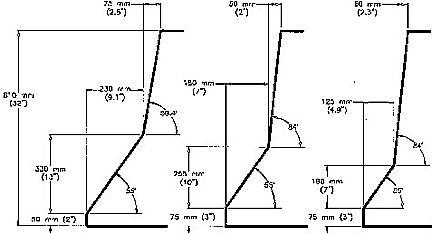
Curve
The signature slopes of Jersey barriers are a purposeful design tested over decades to ensure vehicular safety
The signature Jersey shape is a multi-stage 32-inch high barrier which measures 24 inches at its base and slopes to a width of 6 inches at the top. According to the Federal Highway Administration (FHA) in the first stage of an impact, the front bumper hits the upper sloped face of the barrier, which slides the vehicle upwards and lifts it off the ground. As the bumper collapses under this pressure, the wheels come in contact with the lower sloped portion of the barrier, which reduces the friction between the tires and pavement. This helps to redirect the vehicle and compress the suspension, which lifts and slows the vehicle further. This minimizes injury to passengers and prevents a vehicle from continuing into the path of traffic.
Barrier manufacturers carefully calculate these angles. According to the FHA, “If the vehicle is lifted too high into the air, it may yaw, pitch, or roll, which can cause the vehicle to roll over when the wheels come in contact with the ground again.”
When larger vehicles, such as box trucks or tractor-trailers, impact a barrier, the design of the slopes rolls the truck to a resting place atop the barrier. This keeps the vehicle upright. For this to happen, barriers need a minimum height of 32 inches for box trucks and 42 inches for tractor trailers.
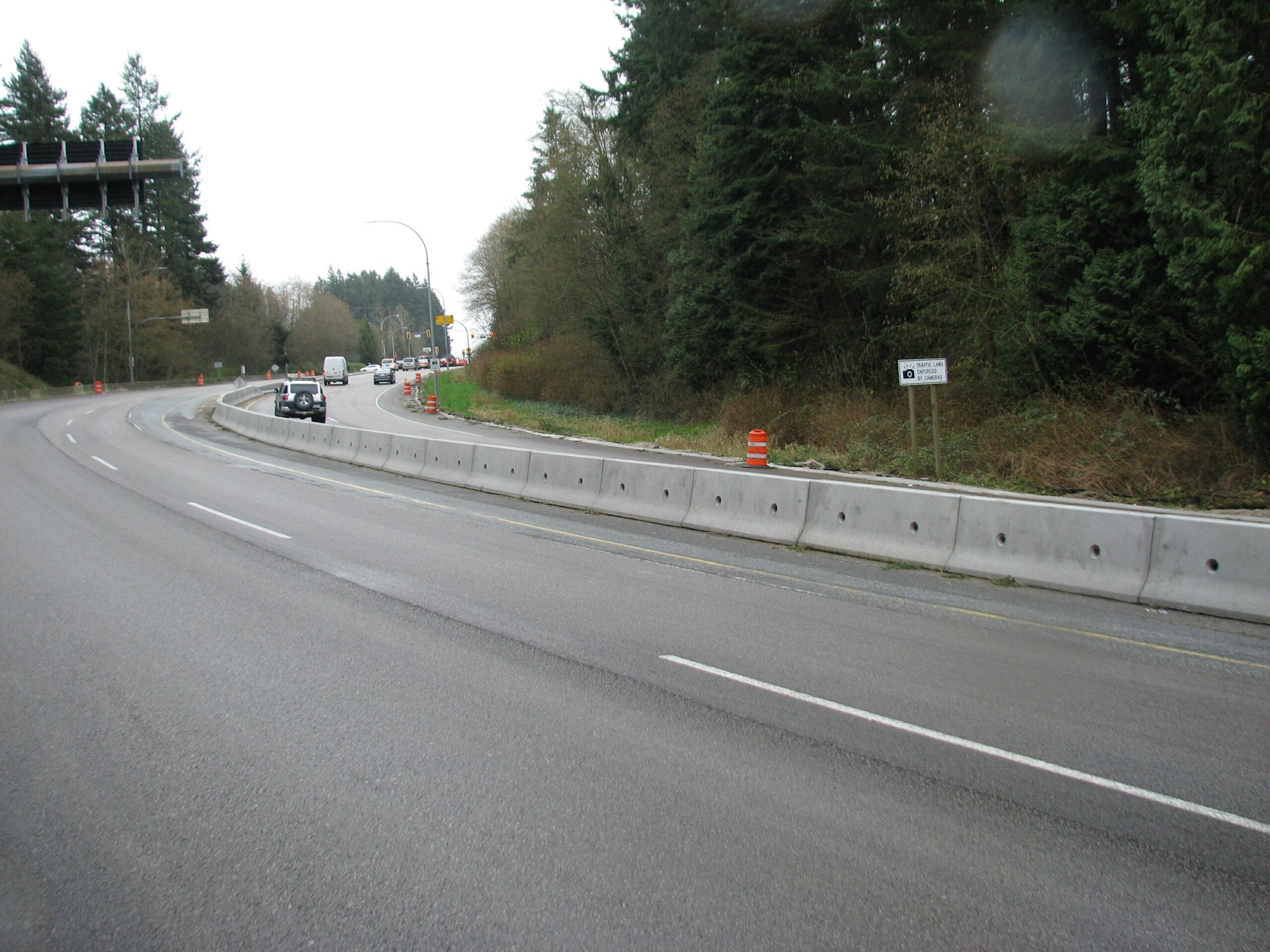
Weight
It’s basic physics — the heavier an object, the more force it can withstand. So, one can imagine that a barrier meant to withstand the force of a tractor-trailer impact must weigh quite a lot. Fortunately, both steel and concrete, the main components of Jersey barriers, are incredibly heavy.
Depending on the exact materials used, barriers can weigh about 400 to 450 pounds per foot. Standard Jersey barriers are 10 feet in length, meaning they can weigh close to 4,000 pounds. Because of this, barriers need to be placed with special equipment.
The extreme weight means that, when hit from parallel traffic, Jersey barriers won’t budge. This not only keeps a vehicle from advancing into oncoming traffic, but it also prevents the impacted vehicle from traveling considerable distances, which in turn keeps the passengers safe from further harm.
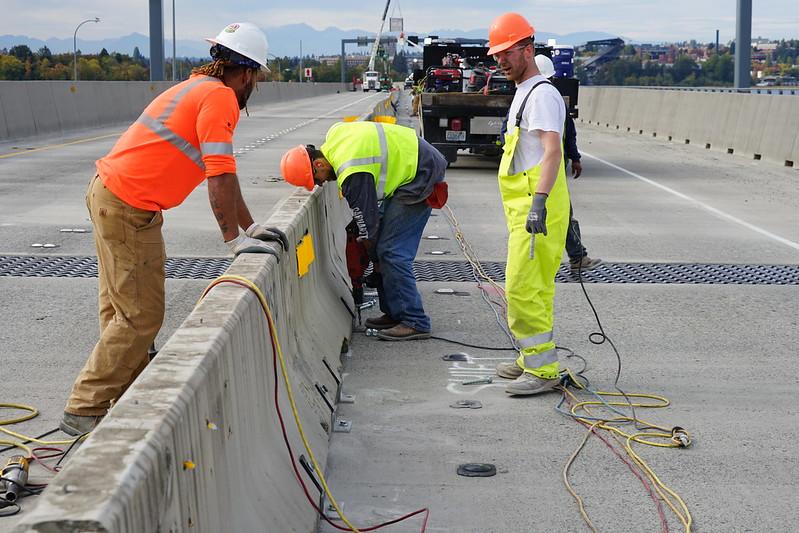
Anchoring & Placement
Jersey barriers are rarely spotted alone. They are typically placed in a chain, forming a continuous barrier.
This strategy serves two advantages. First, it creates a visual barrier. Drivers can more easily follow a road and avoid encroaching upon lanes of oncoming traffic when there is a visible physical barrier between them.
Secondly, it enhances the safety benefits of the barriers. Many Jersey barriers use pin-and-loop connections or JJ-Hooks Connections, which link barrier segments to each other. This further prevents motion upon impact, ensuring that the barrier design works as intended. In this construction, the embedded steel reinforcements protrude from the ends of the barriers and hook together. The FHA notes that pin-and-loop connections can also accommodate curvatures and grade changes in the landscape, making them a popular option for long stretches of road. In many cases, installers can further secure barriers by anchoring them to the ground with steel pins.
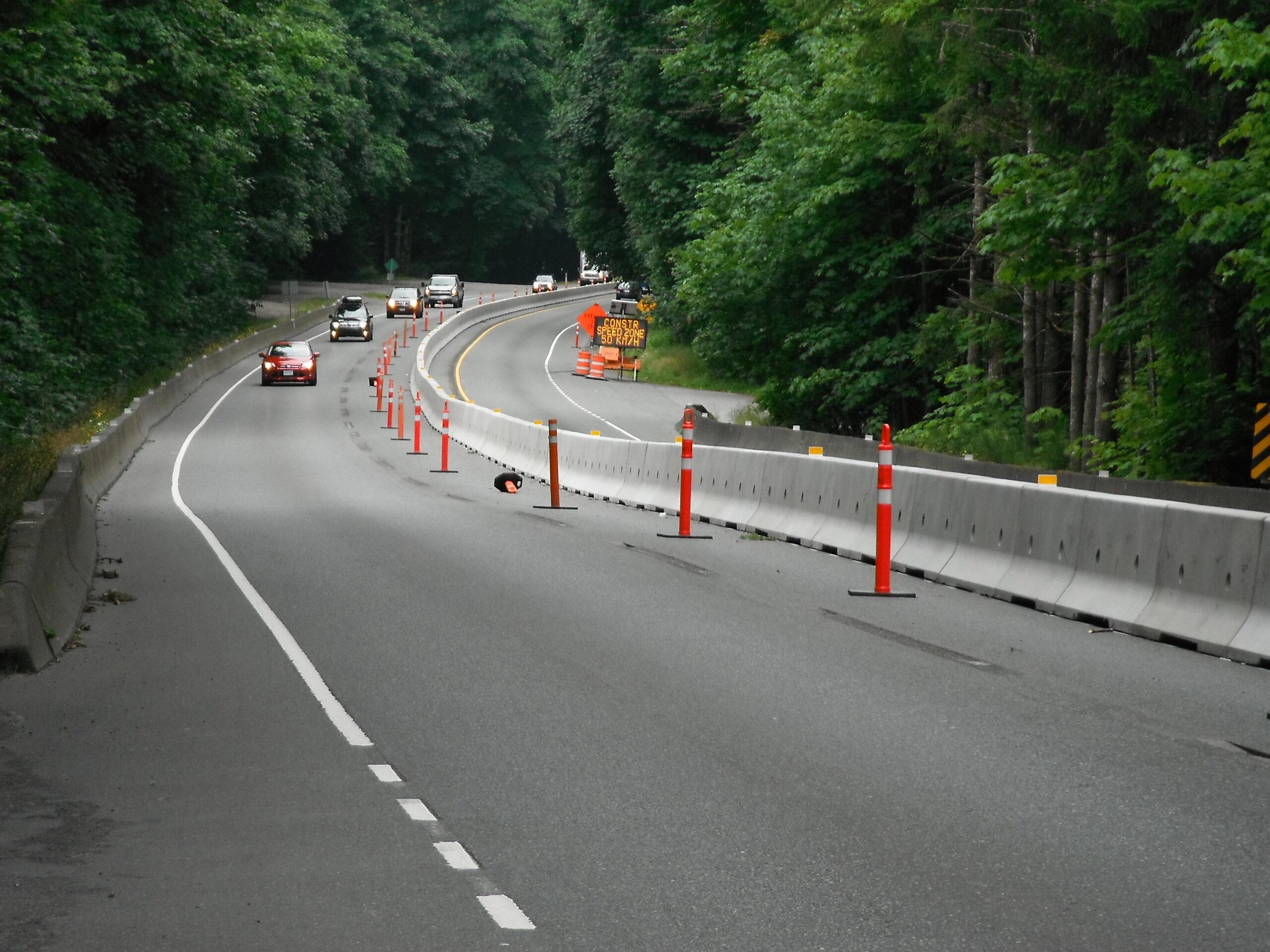
Understanding Safety Ratings
When it comes to understanding how safe barriers are, you’re not on your own. Federal and state authorities, including most Departments of Transportation, have specific standards specifying which materials, designs, and sizes are appropriate for barriers.
Additionally international standards such as the Manual for Assessing Safety Hardware (MASH) Regulation cover crash-testing standards for permanent and temporary highway safety features. These ratings range from TL-1 to TL-6. Each rating corresponds to impacts at different speeds and can help you determine which barrier is right for your needs.
When it comes to traffic safety, no decision should be taken lightly. Fortunately, concrete Jersey barriers have undergone rigorous testing and approval, making them one of the top choices for traffic barrier projects since their inception in the 1940s. When you’re ready to take on your next traffic challenge, don’t navigate this field alone. The team at 48 Barriers will gladly help you pick the safest, highest-quality products for your needs. Give us a call today.